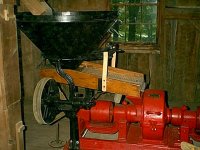 |
On May 12, 2001, The Harrington Community Club hosted The Canadian Chapter of SPOOM's "Spring Millers' Day". The day's activities were to entail removal of the Little Giant Turbine and complete the installation process of the re-worked "Greey's" Oat Chopper, courtesy of Whitelaw Machinery of Woodstock, Ontario.
Guests started arriving at the mill shortly after 10:00 a.m. on this bright but cool day. The idea of the day was to remove the turbine, using the vast experience of the quests present for Millers' Day. It wasn't long before the team assembled, consisting of volunteers from Whitelaw Machinery, the Morningstar Mill in St. Catharines, Ontario, and the Harrington Community Club. The first task at hand was to extract all of the water from the turbine pit. Two submersible pumps made short work of this job, quickly revealing the Little Giant Turbine. It should be mentioned that prior to Millers' Day, the UTRCA (Upper Thames River Conservation Authority) contracted Knoop Excavating to clean out 35 years of organic debris from the turbine pit and millrace. Members of the Harrington Community Club volunteered many hours to assist with all aspects of the preparations for Miller's Day.
Once the water was removed from the pit, a strategy was formulated to remove the fragile turbine. The crew from Whitelaw's quickly rigged a block & tackle system to lift the turbine from its position of 78 years. The turbine was first installed in the mill in the late 1880's and was only removed once for repairs, after the fire of 1923. The mounting hardware on the turbine is made of bronze, which is highly resistant to corrosion, and enabled the bolts to be removed easily. Still, some bolts required heating with oxygen-acetylene torches in order to be extracted. Once all the mounting bolts were removed, the side inspection plates were removed and water was forced through the turbine, flushing years of sediment from its impeller shaft. A block & tackle gear was set up directly above the turbine and the center shaft was slowly separated from the housing, exposing the main running bearing, which is made of wood. The bearing was in surprisingly good condition for its age. The wood used for this bearing is called Lignum Vitae. This wood is described as the densest wood in the world and does not float. Lignum Vitae is harvested in South America.
The impeller shaft was the first to be removed from the mill by carefully rolling it by hand onto long wooden planks. Once outside of the mill, the turbine impeller was attached to a long tow cord and dragged up the steep hillside using a truck. The turbine housing was then removed in much the same fashion. The combined weight of the turbine impeller shaft and housing are roughly 1700 lbs. The turbine was then loaded onto a truck and moved to Whitelaw Machinery. Under closer inspection, it was decided to ship the turbine to Franklin Sandblasting of Woodstock, for precision sandblasting and cleaning. Once this operation was completed, the turbine was once again returned to Whitelaw Machinery, where wear measurements were taken and damaged cast areas were welded.
|