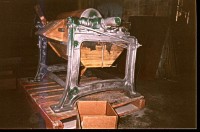 |
Photo shows 1899 Oat Roller sitting on a skid at Whitelaw Machinery in Woodstock, Ont., in a
partially dismantled state (Sand blasted and marked with identification paint).
|
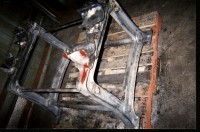 |
Here the Oat Roller is in a completely stripped form. After sand blasting, close
examination detected serious structural cracks in the frame. All required welding was performed.
|
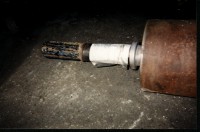 |
In this photo, one of the two rolls are shown with its end shaft repaired by means of
welding new material onto a severely damaged surface. This end shaft was then machined
back to a perfect surface, ready to mate to a pulley. Damage like this is caused by wear
over the years when keyways or wooddrift keys work themselves loose and score the end shafts,
rendering the rolls useless.
|
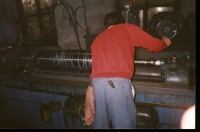 |
After each roll had all necessary repairs performed to each of its end shafts,
] they were installed on lathe for resurfacing! All oxidation and distortment of
the rolls was removed, leaving a perfectly smooth and true surface to work with.
|
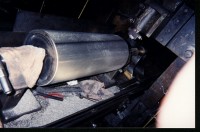 |
In the final stage of the roll preparation, a cut is applied to the roll.
This process is called corigation. The depth and angle of the cut determine the
function of the roll (i.e., grinding corn, flour or other feed). The roll stamping
number remained visible on the oat roller from the Harrington Grist Mill, enabling
the rollers to be re-cut to the original grade.
|
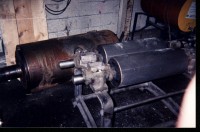 |
With both rolls re-installed on the oat roller frame, the bearing caps were fitted
and packed with a fire retardant caulking. The oat roller was then ready for the pouring
of the moulten babbitt metal.
|
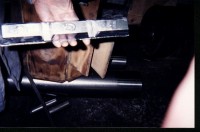 |
The babbitt metal comes in bar form before it is melted and poured into the bearing cage.
|
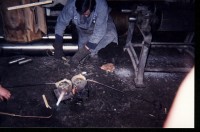 |
The babbitt bars are heated to a moulten state. Eight bars were required to replace the
bearings in the Harrington Grist Mill oat roller.
|
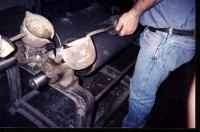 |
Once the babbitt is heated to the correct temperature, it is quickly poured into the
bearing cage. The babbitt is poured simultaneously on either side of the roll to ensure
full coverage of the roll ends and produce a perfect low friction bearing surface.
|
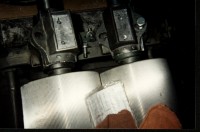 |
Once the babbitt has cooled sufficiently, two small journal holes are drilled into it to
allow for lubrication of the newly poured bearing surfaces.
Each hole is filled with a light weight oil. An oil soaked felt pad is also inserted
on top of the bearing cage to keep dirt and debris out.
|
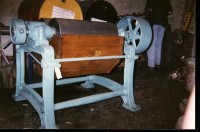 |
After all mechanical repairs were completed on the oat roller, it was
refinished back to its original colours. A light green finish was used on the
frame and drive pulleys, and several coats of varnish were applied to all hardwood surfaces.
|
The Harrington Community Club would like to extend a special thank you to
everyone at Whitelaw Machinery for their outstanding efforts in preserving this
important piece of argicultual history.